Unlimited manufacturing accelerated innovation
Scalable manufacturing services for engineering companies, with Xtproto’s design and manufacturing technology recommendations, get your ideas into production and directly manufactured through our certified advanced manufacturing facilities.
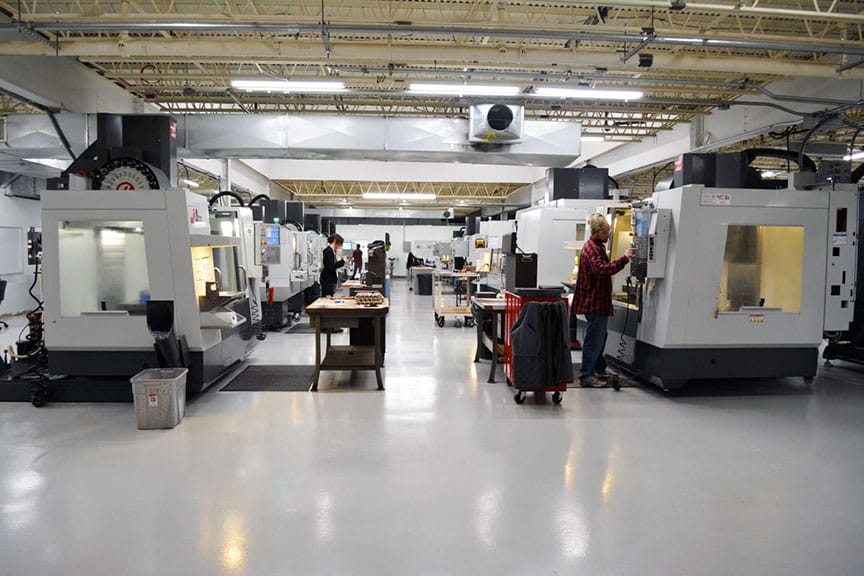
Full ProductLifecycle Support
Xtproto offers full product lifecyclesupport with seamless scaling fromprototyping to production.Ensure your business needs never outpace your production capabilities.
Custom Manufactured Parts Done Right
Discover the Xtproto difference for faster lead times, higher-quality parts, no minimum order quantities, and extensive capabilities. Partner with Xtproto for all of your prototype and production needs.
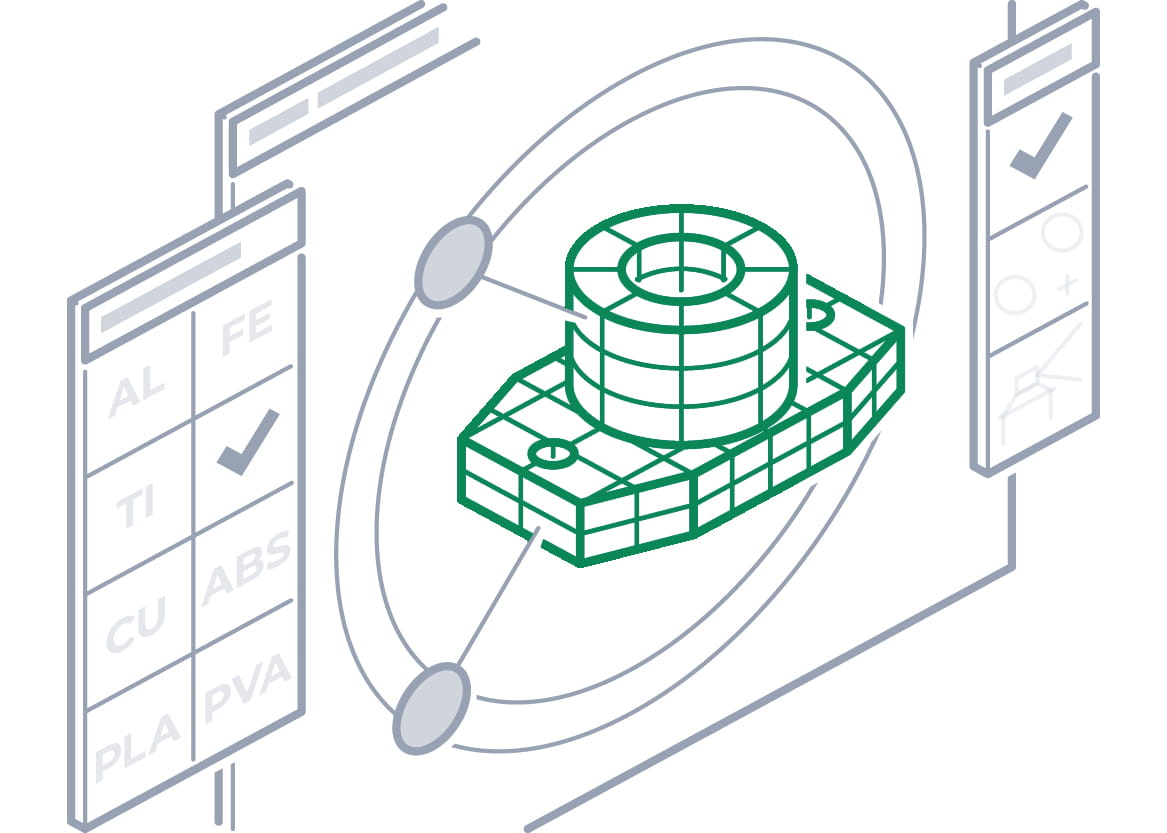
Upload your 3D models and start configuring
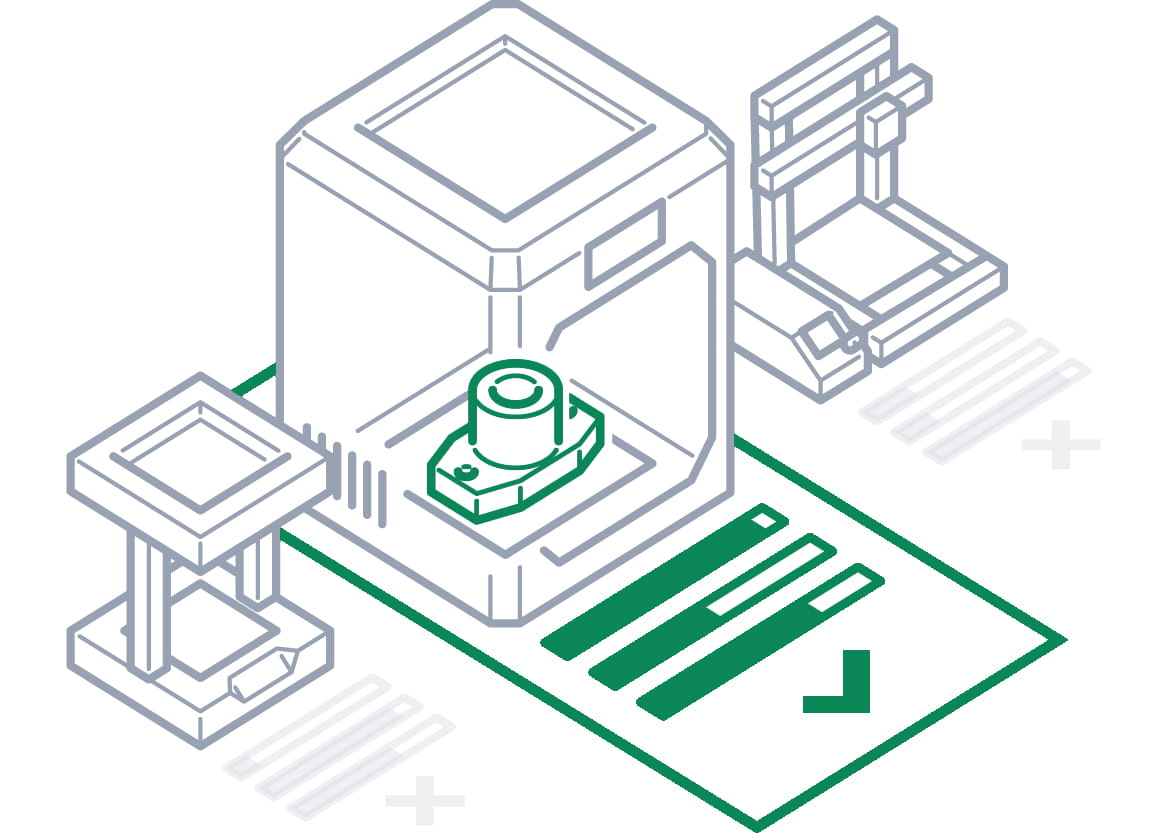
Choose the material, finish and color
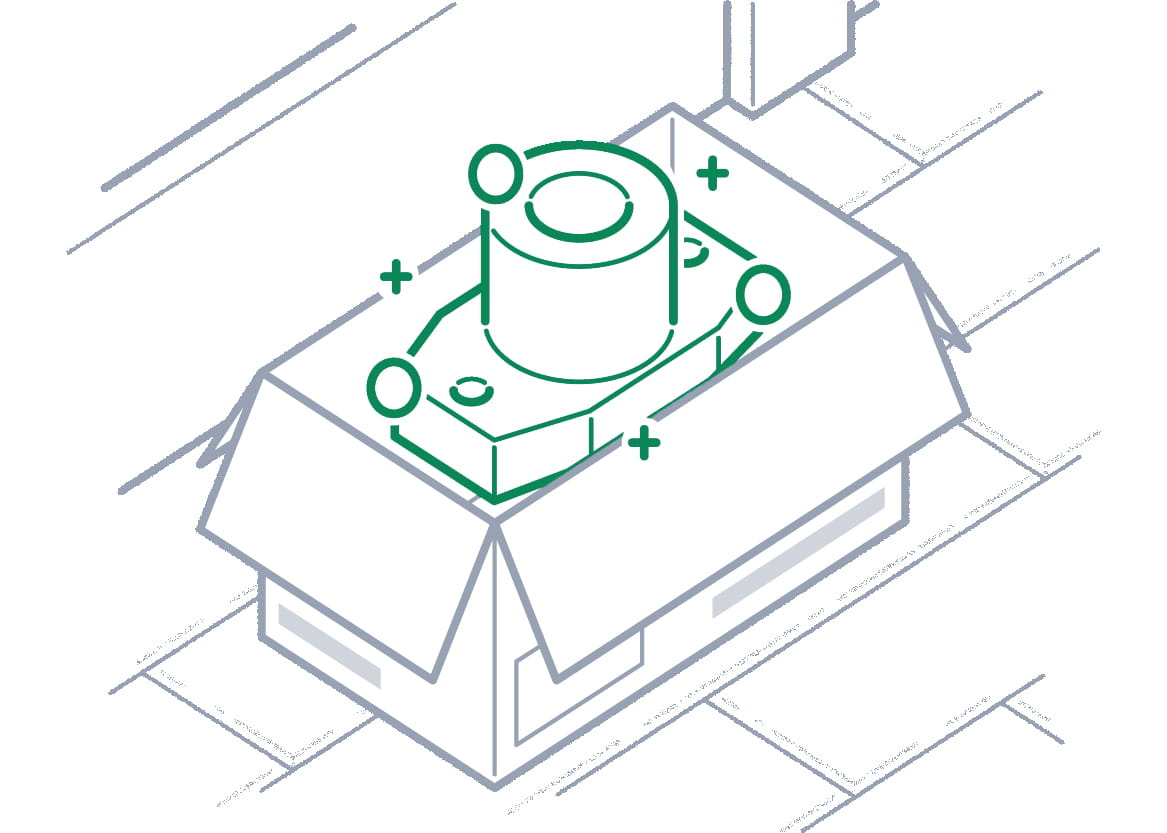
Select the best offer and get your parts delivered
Manufacturing Capabilities to Meet Your Needs
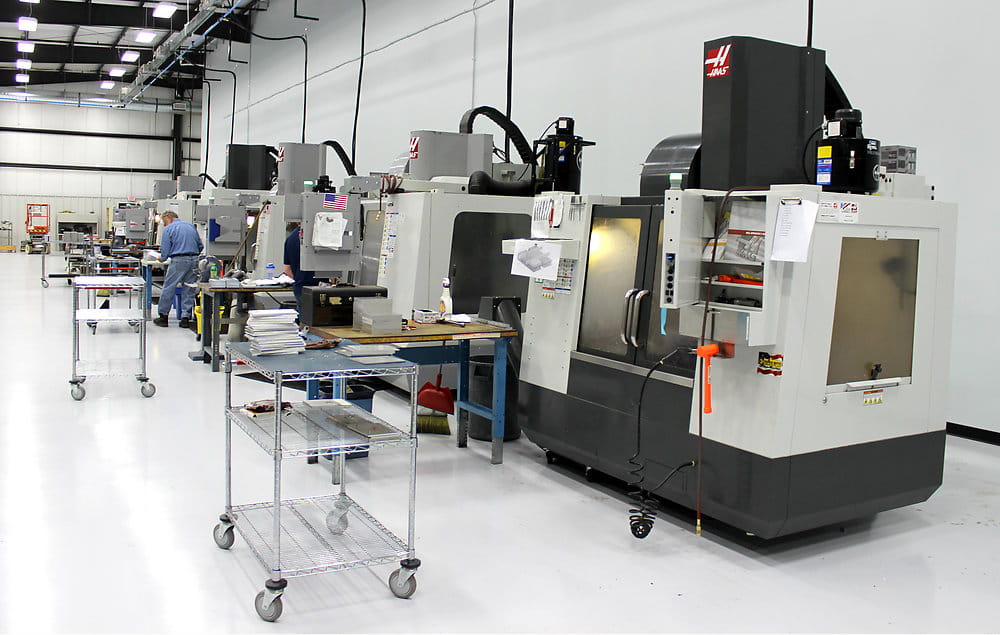
A professional team to provide reliable service and quality
Xtproto’s global team of manufacturing engineers, quality engineers, project managers, strategic procurement managers and logistics experts are committed to ensuring your manufacturing success. Our team works closely with you and our manufacturing partners to achieve the highest standards of service, quality and on-time delivery.
Guided by AI and human support every step of the way
Xtproto guides your decisions with intelligence and engineer team recommendations to help you optimize your design for manufacturability. In addition, Xtproto’s top technical talent is available to answer your questions at any time through our chat system, or for design and manufacturing consultations via Zoom meetings.
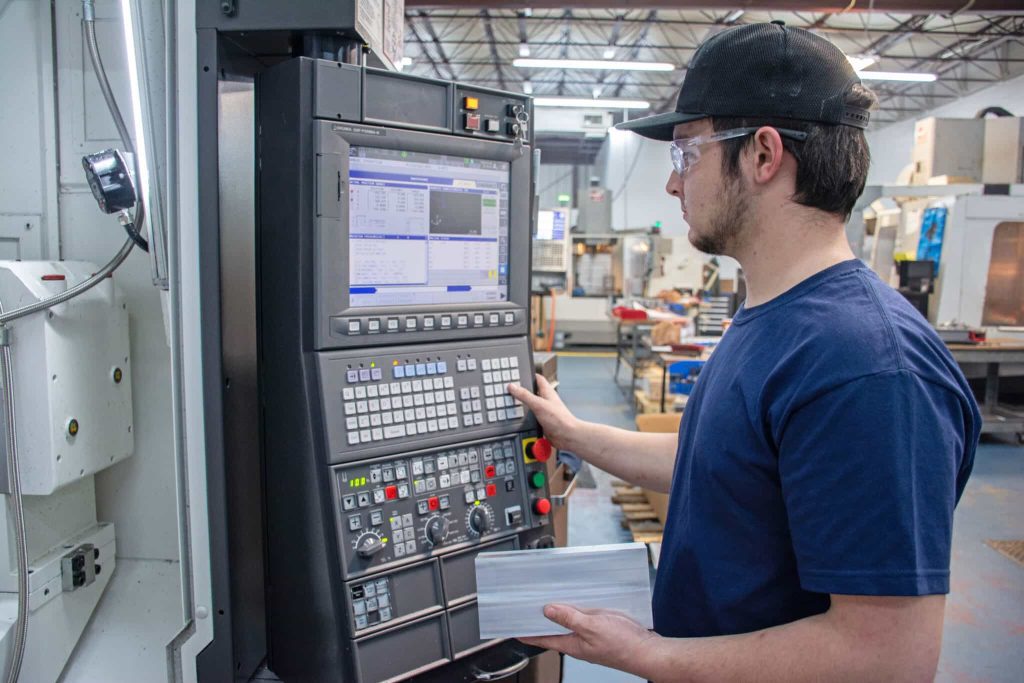
Your Professional Custom Parts Partner
At Xtproto, we want your needs to be at the heart of what we do. Our dedicated team is ready to assist you with any requirements and help you turn your designs into high-quality industrial parts. Whether you are looking for one-off production or batch production, we will help you get industrial parts at the best price.
Our platform can realize any of your needs and ideas, providing a variety of materials and production methods from 3D printing to CNC machining. As long as you need us, we will always be there for you to ensure that you return satisfied!
Get started and turn your ideas into reality
Submit a production inquiry. Ideal for prototypes and low-volume production as well as complex and high-volume applications.