Die Casting
XTPROTO has the scale and experience to provide you with the best die cast parts. Our complete parts system includes casting, machining and finishing.
Die Casting Manufacturer
XTPROTO offers a full range of premium die casting services for both low and high volume production of metal parts. Our services are available for a variety of applications and include part casting, mold making, post machining and finishing services for completed parts.
Our die casting solutions work with a wide range of metal alloys, ensuring your project will be perfect for your end use. We manufacture parts with extreme dimensional accuracy, tight tolerances, and thin wall thicknesses where specified. From aluminum to magnesium and zinc, our casting machines and durable, finely detailed molds are our unique value proposition, ensuring we deliver parts of the highest standard and quality.
At XTPROTO, we can use our die casting services to reduce your unit part cost. We can manufacture steel molds with rapid tooling to fit budget constraints when producing small batches. From wet painting and powder coating to polishing and anodizing, our premium finishing solutions will enhance the overall appearance and beauty of your parts.
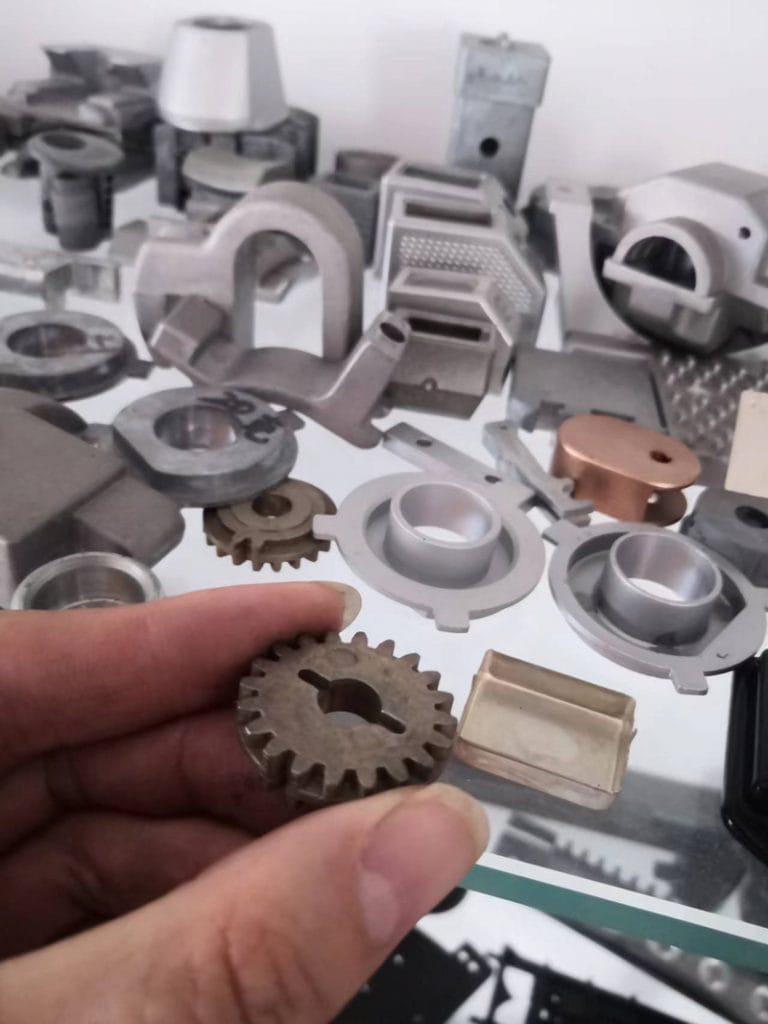
Why Choose XTPROTO?
- Use state-of-the-art die casting technology, including die casting machines, to get your product done right, on time.
- We adhere to strict Design for Manufacturing (DFM) standards – meaning we help you design your parts and optimize your mold design to simplify manufacturing. This reduces our startup, material and functional costs, providing you with cost-competitive manufacturing services.
- Our state-of-the-art die casting technology is compatible with a wide range of materials, including zinc and aluminum alloys.
- We complement our precision die casting services with a comprehensive range of surface machining and finishing processes, such as plating, painting, polishing and powder coating. Our facility is also equipped with state-of-the-art CNC machines to handle complex part design and assembly.
- Our die casting services are ideal for mass production of both simple and complex parts, and are perfect for customers looking to scale up their product development projects.
- We are located in New Zealand and are not far from shipping ports, allowing us to provide you with fast manufacturing services.
- We have been in business for nearly 20 years, providing unparalleled manufacturing services to customers from a wide range of industries.
Our Casting Equipment and Capabilities
Our machines range from 280 tons to 1,750 tons and can mold parts up to 13 kg (about 29 pounds) and 1,500 x 1,100 mm (59 in x 43 in) in size. Our in-house tool shop gives us full control over the entire process and ensures that only the highest quality materials are used. Our experienced engineering staff uses advanced mold flow software to control porosity in large open geometry parts.
Every part we produce has a documented process control procedure to ensure batch-to-batch product consistency. In addition, our ISO material control system ensures that there is no metal contamination. We offer a range of casting processes: air solidification, continuous, counter pressure, densification, high pressure, hot chamber, impregnation, low pressure, pressure casting, Shore process, static, tilt pouring, vacuum and vacuum impregnation.
Specific mold types used include ceramic, upper and lower molds, high pressure molds, low pressure molds, plaster, precision ceramic shell, shell and solid. Available process materials include dry sand, foam, green sand, oil sand, sand and wax.
All parts are held to tight tolerances to meet or exceed stringent industry standards. We can accommodate a wide range of production volumes, whether the customer requires a prototype, a small or large batch order, or a comprehensive order. Lead times are based on the job, but rush orders can be accommodated.
Our manufacturing facilities are ISO 9001:2008/TS 16949 certified and adhere to multiple industry standards—including those set by the American Society of Mechanical Engineers (ASME), the American Welding Society (AWS), and the Food and Drug Administration (FDA), to name a few.
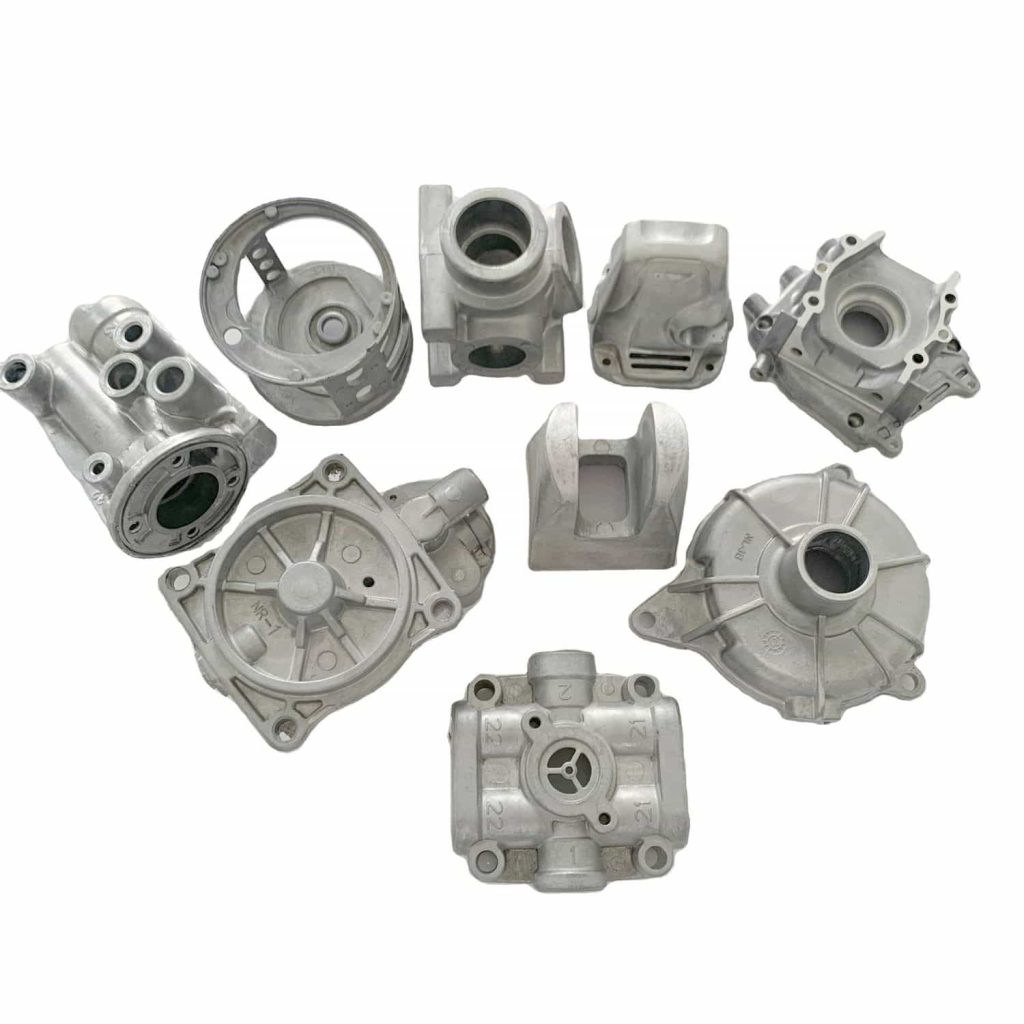
Die Casting Processes
There is no one process that is right for all projects. Every project is different, which is why XTPROTO offers multiple solutions for all die casting needs. This ensures that the right process is always used for the right application. At XTPROTO, we offer several different types of die casting processes.
- Cold Chamber Die Casting: Versatility Unleashed. Ideal for high-melting-point metals like aluminum, this method reduces machine corrosion, offering versatility in material choices.
- Hot Chamber Die Casting: Swift and Efficient. The most popular method, especially for lower-melting-point metals like zinc, this approach ensures efficiency without compromising precision.
- High-Pressure Die Casting (HPDC): HPDC utilizes higher injection pressures, resulting in improved part density, reduced porosity, and enhanced mechanical properties.
- Vacuum Die Casting: This method minimizes gas porosity in the final product by removing air from the die cavity before metal injection, ensuring higher quality components.
- Multi-Slide Die Casting: Multi-slide die casting allows to produce complex and multi-cavity parts in a single operation, increasing efficiency and reducing production time.
Offshore Cost Advantages with Quality Assurance and Customer Service
XTPROTO leverages competitive overseas labor costs and engineering and logistics support. Our team will create your custom sourcing solution to ensure reliable, economical die cast parts and products. We provide our valued customers with the competitive advantages that come from our established manufacturing operations while ensuring globally competitive pricing, delivery times, and quality from world-class manufacturers.
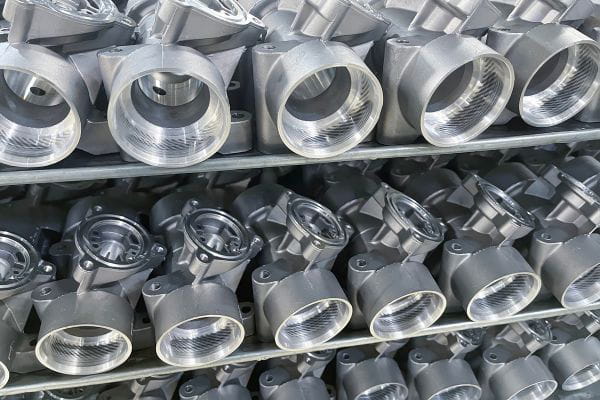
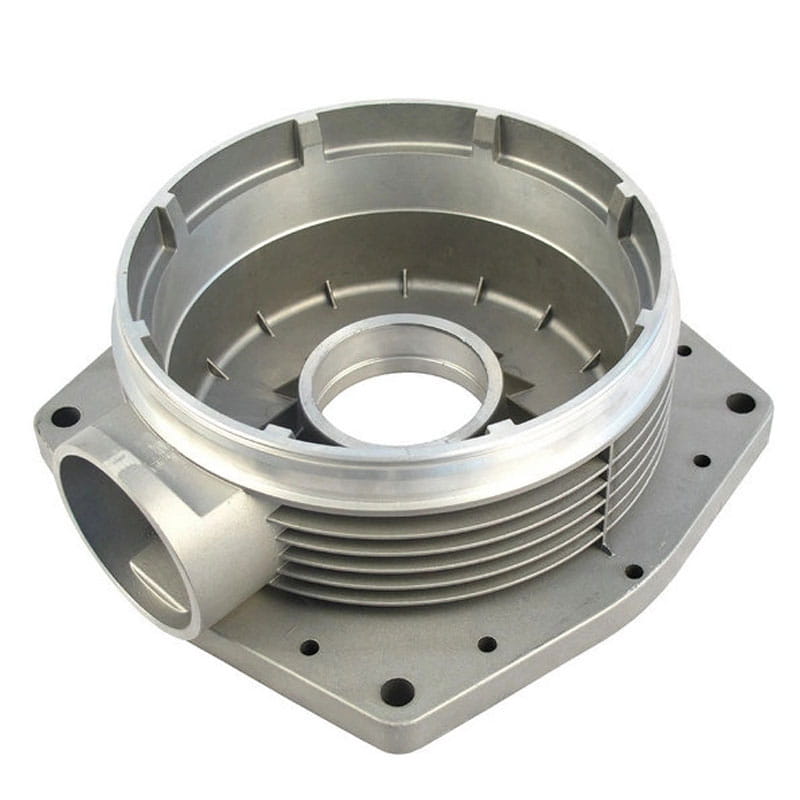
In-house Mold Manufacturing and Value-added Services
The success of your die casting project depends on the quality of your molds, and our mold manufacturing capabilities are unmatched in Asia. Upon receiving your order, we will:
- Perform a complete manufacturing design review of your CAD files.
- Verify that the tooling and product raw materials are compliant.
- Use our multi-axis imported CNC machines to create cores and cavities.
- Use careful heat treatment to temper the molds.
- Perform process control when casting parts.
- Provide any necessary post-processing or treatment.
- Expertly inspect and measure finished parts to meet and exceed your specifications.
Die Casting Materials
When manufacturing with die casting, there are several different metal materials to choose from. The material you choose will depend on your intended use for your product. For example, cast aluminum parts are common in aerospace or automotive applications where corrosion resistance and weight reduction are important factors. You can learn more about the main types of die casting materials we offer in the section below. If you have a specific material requirement, let us know!
- Aluminum
- Zinc
- Magnesium
- Copper
- Tin
- Lead
Finishing Services
At XTPROTO, our metal castings can be treated with a variety of finishing solutions to get your parts to their best in terms of appearance and performance. Some of our die casting finishing techniques include:
- Standard
- Sandblasting
- Grinding
- Painting
- Powder coating
- Electroplating
- Polishing
- Anodizing
What is Die Casting?
Die casting is a manufacturing process that uses a mold (also called a die) to produce metal parts. The process involves forcing molten metal into a mold cavity (under high pressure) to create the desired metal part.
The mold consists of two halves (usually made of heat-resistant steel) that form a cavity into which the liquid metal is forced at pressures ranging from 1,000 to 20,000 psi. There are two types of die casting processes – hot chamber die casting and cold chamber die casting.
Both processes are suitable for producing high-quality die castings; they differ slightly in their casting methods. The ideal die casting process depends primarily on the type of metal and part you are looking to create.
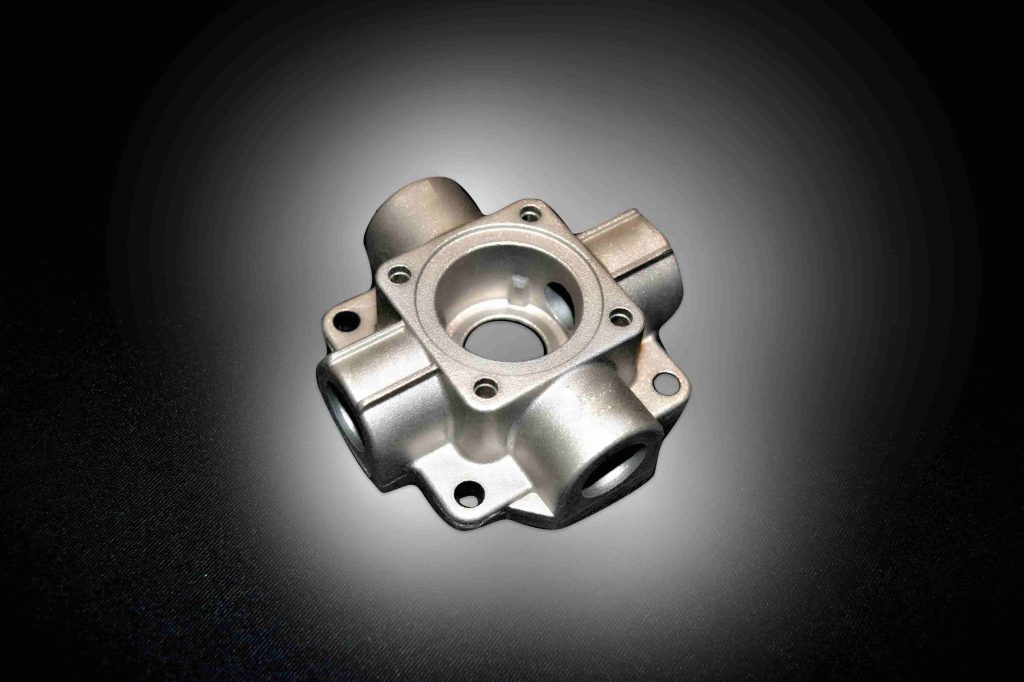
Is Die Casting Right for Your Product?
The die casting process is the fastest option for producing precise nonferrous metal products. Because this method uses reusable molds, parts can be produced at high speeds and have the flexibility to manufacture a wider range of shapes and sizes than other casting methods.
Die casting can be fully automated, and its reusable molds also make it an affordable option. The technology is used to manufacture commercial, consumer, and industrial products. Die casting is ideal for medium-sized parts with more complex structures.
How to get started with us?
Our die casting services are unmatched, with the ability to create complex shapes, use a wide range of alloys, and achieve fast production. If you are ready to get started, choosing materials and an experienced injection molding partner is crucial. You can easily navigate with the help of our experienced professionals who will guide you to find the best solution for your specific project.
When you work with XTPROTO, you can get die casting services in materials ranging from aluminum to magnesium and zinc alloys. You can get started by sending an inquiry and drawings to our company. After careful consideration, our managers will contact you and then begin the amazing realization process. Our state-of-the-art facilities and cutting-edge technology ensure that each casting is a masterpiece and meets the most stringent quality standards.
Request a Free Die Casting Quote Now
Once we receive your drawings, our engineers will immediately analyze your custom die casting. We proactively work with you to clarify all details and then provide a quote that is both economical and accurate.