Urethane Casting
XTPROTO’s mission is to provide convenient and superior manufacturing services. If your business requires mass production of parts, traditional methods such as polyurethane casting may be the best choice to achieve the highest speed and output.
Urethane Casting Supplier
XTPROTO has many years of experience in Urethane Casting and can process any component in Urethane Casting, from a simple gasket to the most complex housing for a robotics project. We support rigid, elastomeric and silicone materials and can paint, install hardware and even post-process your Urethane Casting so that you get the exact component you need. Urethane Casting requires a high level of communication with the customer regarding design, first article approval and balancing.
Our Urethane Casting technology provides designers and product engineers with the flexibility to manufacture small quantities of rigid or flexible end components at mass production quality.Urethane Casting technology does away with molds, instead using 3D printed master parts to replicate parts and silicone molds to manufacture small batch units of parts.
XTPROTO’s Urethane Casting is a reliable and cost-effective way to make master models and cast high-end plastic prototypes and final parts. Our Urethane Casting services are designed to bridge the production gap from prototype to mass production, making parts available for a variety of testing, crowdfunding, marketing and demonstration purposes.
Combined with our best-in-class finishing services, XTPROTO can get you castings in as little as 7 days. We are fully capable of handling all your silicone molding needs, using our experience in general manufacturing to manufacture and finish your parts to the highest standards. Our polyurethane and Urethane Casting solutions are ideal for quickly and economically manufacturing prototypes in quantities as small as one to a hundred.
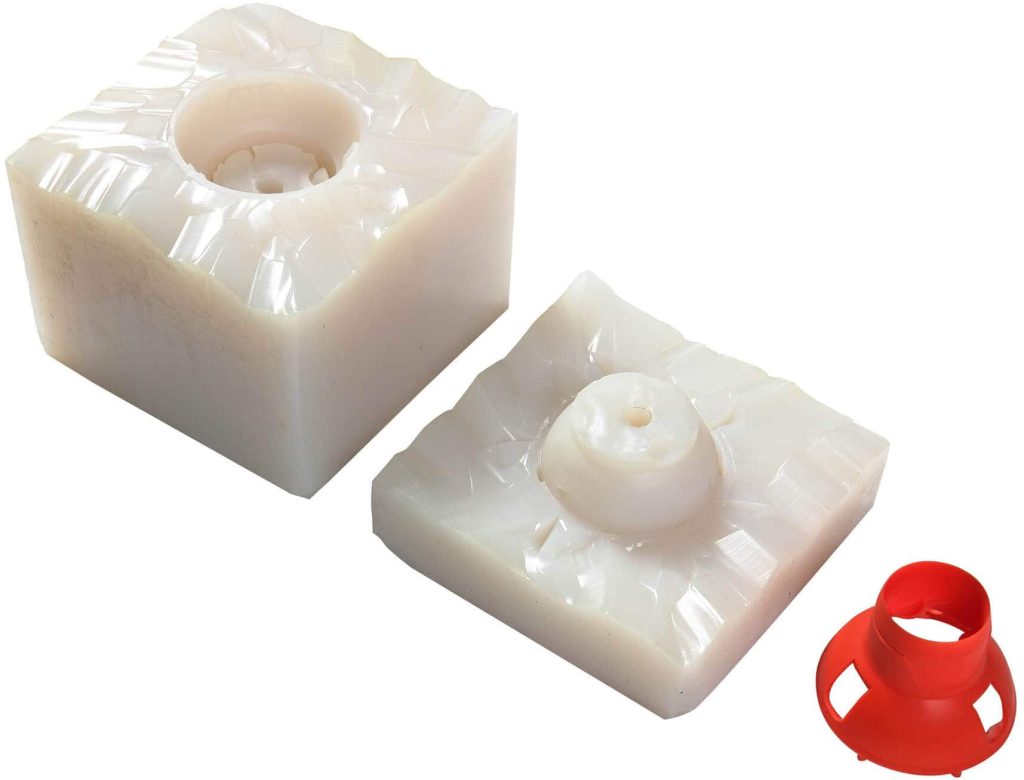
Why XTPROTO for Cast Urethane?
- No-compromise quality: Rigid rubber? Tough plastics? We’ve got you covered. Our parts meet your industry’s highest standards.
- Fast turnaround, no delays: Ditch slow tooling. Our 3D printing and molds get your parts to you quickly, without sacrificing quality.
- Precision you can trust: Expect minimal shrinkage and consistent dimensions thanks to our 25 years of experience.
- More than just tough: Get color-matched, clear, or painted parts. We’ll make your final product look flawless.
- Perfect for small batches: Cast urethane shines for low volume production runs, bridging the gap between prototypes and mass production.
Validate part designs without hard tooling
Are you planning to produce a part via injection molding, but not yet ready for machining? XTPROTO’s polyurethane casting service is an ideal way to quickly produce a small number of parts for functional and cosmetic testing. Depending on the part geometry and the number of parts required, it can also be faster and cheaper than additive manufacturing.
Urethane Casting Options
Urethane is one of the most versatile materials available, and can be manipulated to provide a wide range of properties, textures, hardnesses and so on. At RevPart, we take pride in our versatility, and are ready to work with you to overcome any challenges in creating the parts you need.
Color:
We can produce exactly the shade that is needed through our wide variety of paints.
Finishes:
The urethane casting process is ideal for custom finishes and textures — due to the nature of the 3D printed original pattern and the qualities of the silicone rubber mold. We can texture the mold and part according to any SPI finish or MT finish, as well as any custom design you may require.
Resins:
Urethane is versatile and able to nearly reproduce the qualities of a number of materials, including ABS, PP and PE. When ABS-like, PP-like and PE-like prototypes are needed, you save on the cost of low-volume quantities of those materials by making use of the versatility of urethane.
Value-added options:
When additional requirements beyond urethane casting are needed to create your part, we can provide them, including spray painting, pad printing, screen printing and more.
Urethane Casting Technical Specifications
- Standard Lead Time: Up to 10 copies within 14 days
- Standard Tolerance: ±0.3% (with a lower limit on ± 0.3 mm on dimensions smaller than 100 mm)
- Minimum Wall Thickness: To ensure that the mold is filled properly, a wall thickness of at least 0.75 mm is necessary. For best results, we recommend a wall thickness of at least 1.5 mm
- Maximum Part Dimensions: The size of the mold is limited by the dimensions of the vacuum chamber (1900 x 900 x 750 mm) and by the volume of the product (maximum volume: 10 liters)
- Typical Quantities: Up to 25 copies per mold (depending on the mold’s complexity and the casting materials)
- Surface Structure: High-quality surface finish comparable to injection molding
Urethane Casting Molds
The molds we make are soft tools, made primarily of silicone or polyurethane, meaning they are temporary molds. Standard molds can produce approximately 25 shots per cavity. Production molds can produce more parts per cavity depending on geometry, quantity, and material. For more complex parts and/or production parts, we will create a complete mold with core halves and cavity halves (similar to injection molding). Each mold is created based on the requirements of the part and project. We make single cavity, series molds, or multi-cavity molds based on the most efficient process to get your part done quickly and correctly. Here are the different types of molds we can create:
- 3D Printed Molds: Perfect when you need a part quickly, a non-critical, non-aesthetic functional part, and only care about functionality and fast delivery.
- Soft Prototype Molds: Perfect for rapid prototyping or rapid production of parts without strict requirements. It is the perfect blend of quality, fast delivery, and low cost.
- Soft Production Molds: Uses higher grade mold materials to produce better quality, more repeatable parts to meet critical features and tolerances. Cost and delivery time are slightly longer.
- Rigid Production Tooling: Achieve higher throughput and repeatable high-tolerance cast polyurethane production with rigid tooling (aluminum or rigid paperboard). Cost and lead time are much higher than other options, but more parts per mold.
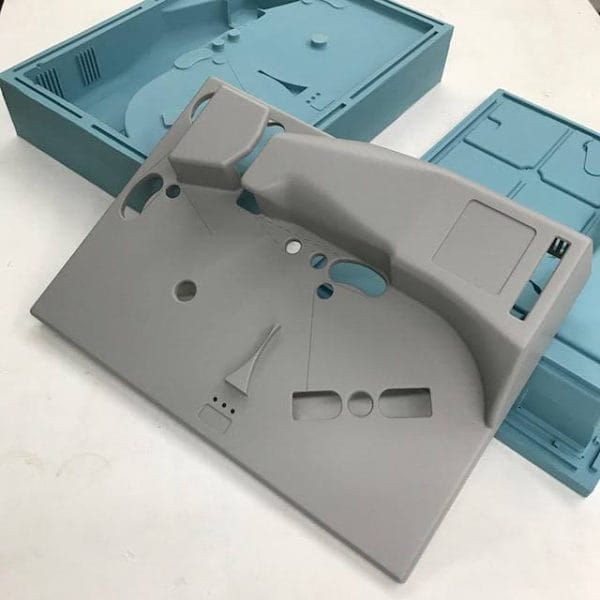
How Does Urethane Casting Work?
The urethane casting process is simple:
- A master pattern is designed using 3D computer-aided design (CAD) software.
- The master pattern is created using CNC Machining or Stereolithography (SLA). Alternatively, it may be supplied by the client.
- The master pattern is then placed in liquid silicone to form a mold.
- After the silicone mold has fully cured, it is halved and the master pattern is removed. The cavity left behind is what is used for casting.
- Urethane and other resin materials are added to the mold tool and cured.
- The completed part is removed from the mold and the process is repeated.
Benefits Of Urethane Casting
- Low cost for molds
- Molds can be made in a few days
- Many types of polyurethane resins are available for casting, including overmolding
- Cast copies are highly accurate with excellent surface texture
- Molds are durable for 10 or more copies
- Perfect for engineering models, samples, rapid prototypes, bridge to production
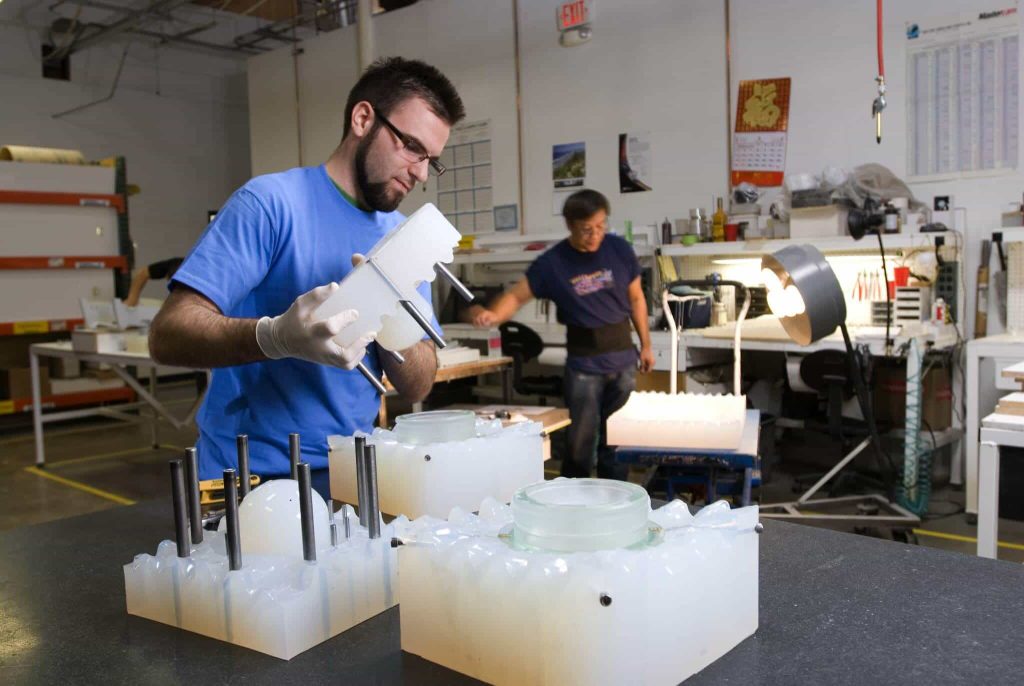
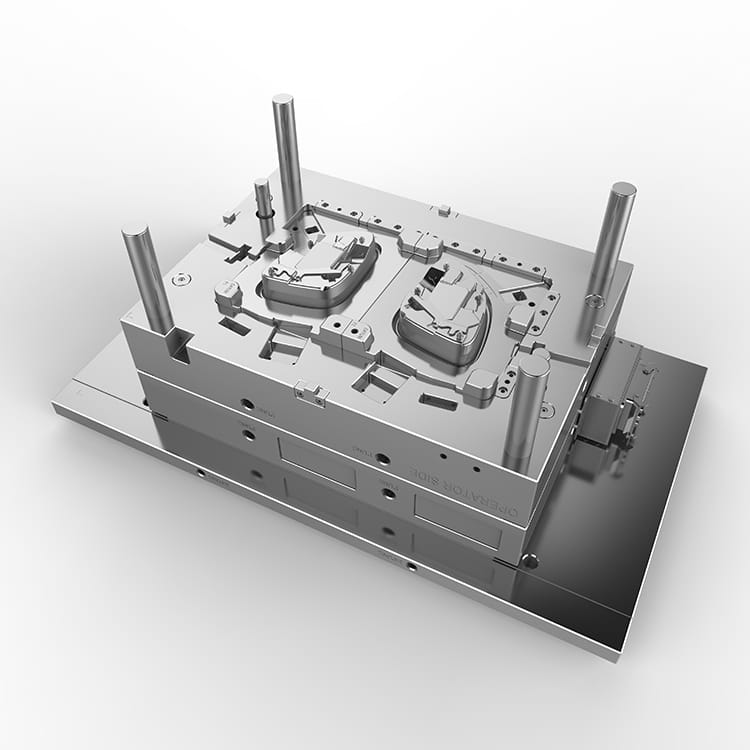
A High-Quality Alternative to 3D Printing and Injection Molding
Polyurethane and silicone casting are a versatile middle ground between 3D printing and injection molding that can offer the best of both worlds. Modern material advances have made silicone and polyurethane cast parts comparable in quality to injection molded parts. At the same time, these cast parts can be produced in small batches at a faster rate and lower cost than injection molding.
Compared to 3D printing, silicone and polyurethane casting materials have a wider range of chemical, thermal, and mechanical properties than 3D printing plastics. Cast parts also offer better value for medium to large parts because they are not limited by print bed size. Finally, cast parts have a superior finish and fine detail compared to 3D printed parts, which means they can accurately create the look and feel of consumer products without any additional finishing.
Designing Cast Parts
When designing parts for silicone and cast urethane production, it is critical to consider the properties of the materials. Silicones are known for their flexibility, elasticity, and ability to withstand high temperatures, while cast urethane parts are durable and wear-resistant.
When designing parts for silicone production, it is important to ensure that the design is easy to demold. This means avoiding chamfers or sharp corners that could cause tearing during demolding. It is also critical to incorporate fillets and draft angles for good material flow.
It is also critical to optimize the design of the molding process for cast urethane. This includes ensuring appropriate wall thickness, providing gates and runners for material flow, and utilizing cavities that allow for quick removal of cast urethane parts.
In both cases, the design must be reviewed with the manufacturer to ensure it is appropriate for the selected material and production process.
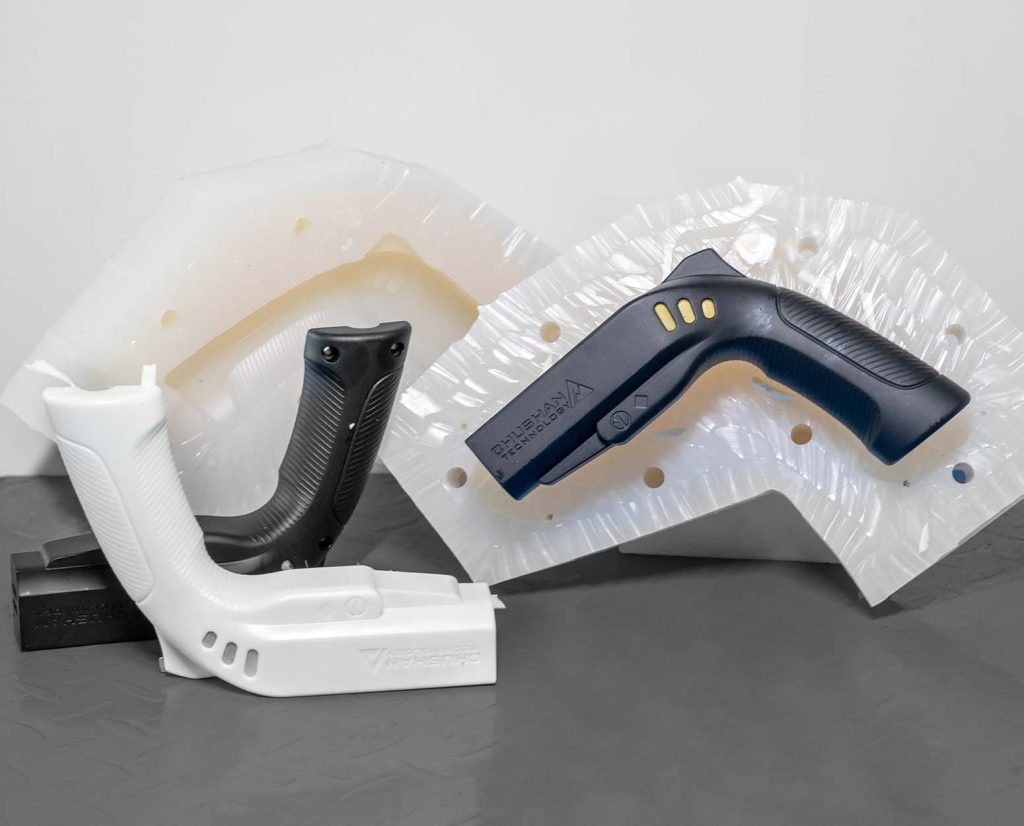
Choose XTPROTO for your next Silicone or urethane casting Project
If your project requires Silicone or urethane casting services, you should consider working with XTPROTO. XTPROTO offers high-quality casting services with fast turnaround times. Our experienced team excels in crafting molds and castings of all sizes, complexities, and purposes. We use advanced equipment and techniques to ensure precise and accurate results. In addition, XTPROTO uses top-quality materials to ensure that its castings are durable, long-lasting, and can withstand a variety of conditions and environments. In addition, our team is committed to providing excellent customer service and works closely with our customers throughout the casting process to meet their needs and specifications. At XTPROTO, you can expect professional service and high-quality castings to meet your project needs.
Ready to Get a Urethane Casting Quote?
From design to prototyping and production, our team of engineers is ready to help you turn your ideas into reality.